حل مشکل کارایی فرآیند دو اثر مثبت دارد.
اول از همه، وارد کردن پردازش کویل به فرآیند - همانطور که دیدیم - باعث صرفه جویی در مواد خام می شود که حتی می تواند بیش از بیست درصد برای همان مقدار محصول باشد و این به معنای حاشیه مثبت و جریان نقدی است که بلافاصله در دسترس است. به شرکت.
این ممکن است بسته به بخش و استفاده متفاوت باشد: در هر صورت، این موادی است که کارآفرین و شرکت دیگر مجبور به خرید آن نیستند و همچنین زباله ها نیازی به مدیریت یا دفع ندارند.
کل فرآیند بسیار سودآورتر است و نتیجه مثبت را می توان بلافاصله در صورت سود و زیان مشاهده کرد.
علاوه بر این، شرکت با خرید مواد خام کمتر، به طور خودکار فرآیند را پایدارتر می کند، زیرا آن ماده خام دیگر نیازی به تولید پایین دستی ندارد!
بهره وری انرژی یکی دیگر از عناصر مهم در هزینه هر چرخه تولید است.
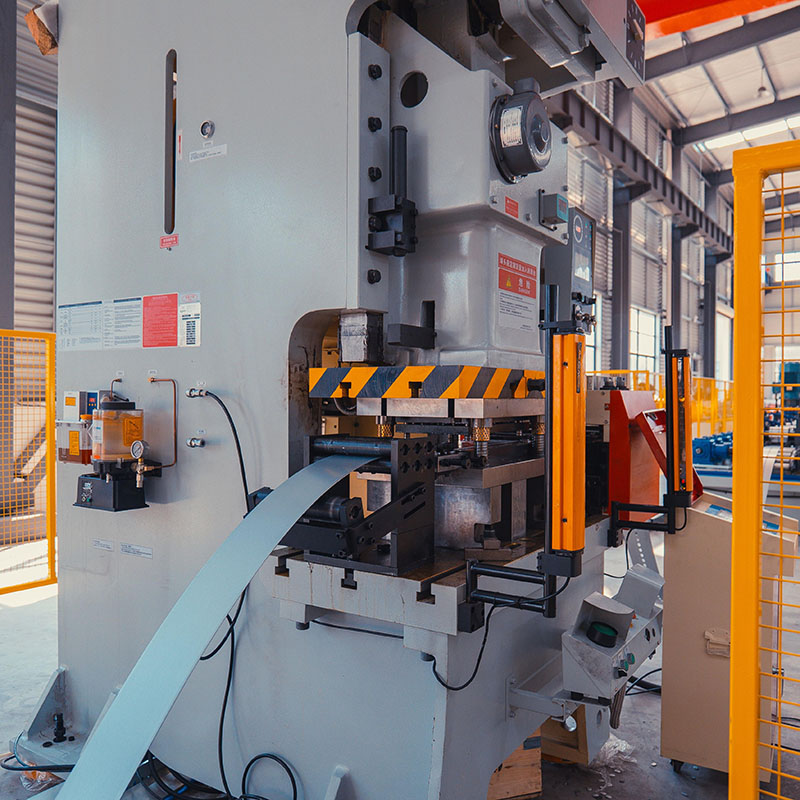
در یک سیستم تولید مدرن، مصرف دستگاه رول فرمینگ نسبتا کم است.به لطف سیستم Combi، خطوط را می توان با چندین موتور کوچک که توسط اینورتر هدایت می شود (به جای یک موتور ویژه بزرگ) مجهز کرد.
انرژی مورد استفاده دقیقاً همان چیزی است که در فرآیند شکلدهی لازم است، به علاوه هرگونه اصطکاک در قطعات انتقال.
در گذشته، یک مشکل بزرگ در ماشینهای برش سریع، انرژی تلف شده از طریق مقاومتهای ترمز بود.در واقع، واحد برش با صرف انرژی زیاد، به طور مداوم شتاب و کاهش می یابد.
امروزه، به لطف مدارهای مدرن، میتوانیم انرژی را در حین ترمزگیری جمع آوری کنیم و از آن در فرآیند رولسازی و در چرخه شتاب بعدی استفاده کنیم و بخش زیادی از آن را بازیابی کنیم و در اختیار سیستم و سایر فرآیندها قرار دهیم.
علاوه بر این، تقریباً تمام حرکات الکتریکی توسط اینورترهای دیجیتال مدیریت می شوند: در مقایسه با یک راه حل سنتی، بازیابی انرژی می تواند تا 47 درصد باشد!
یکی دیگر از مشکلات مربوط به تعادل انرژی یک ماشین وجود محرک های هیدرولیک است.
هیدرولیک هنوز هم عملکرد بسیار مهمی را در ماشینها انجام میدهد: در حال حاضر هیچ محرک سروو الکتریکی وجود ندارد که بتواند نیروی زیادی را در فضای کم ایجاد کند.
در مورد دستگاه های پانچ با کویل، در سال های اولیه ما فقط از سیلندرهای هیدرولیک به عنوان محرک برای پانچ ها استفاده می کردیم.
ماشینآلات و نیازهای مشتری به رشد خود ادامه دادند و اندازه واحدهای قدرت هیدرولیک مورد استفاده در ماشینها نیز افزایش یافت.
واحدهای برق هیدرولیک روغن را تحت فشار قرار می دهند و آن را در کل خط توزیع می کنند و در نتیجه سطوح فشار کاهش می یابد.
سپس روغن گرم می شود و انرژی زیادی هدر می رود.
در سال 2012، ما اولین دستگاه پانچ با کویل برقی سروو را به بازار معرفی کردیم.
در این دستگاه، ما بسیاری از محرکهای هیدرولیک را با یک سر الکتریکی که توسط یک موتور بدون جاروبک مدیریت میشود، جایگزین کردیم که تا 30 تن تولید میشد.
این راه حل به این معنی بود که انرژی مورد نیاز موتور همیشه فقط انرژی مورد نیاز برای برش مواد است.
این دستگاه های سروالکتریک نیز 73 درصد کمتر از نسخه های هیدرولیک مشابه مصرف می کنند و مزایای دیگری نیز دارند.
در واقع، روغن هیدرولیک تقریباً هر 2000 ساعت باید تعویض شود.در صورت نشتی یا شکستگی لوله ها، تمیز کردن و پر کردن مجدد زمان زیادی طول می کشد، بدون اینکه به هزینه های نگهداری و بررسی های مربوط به سیستم هیدرولیک اشاره کنیم.
با این حال، راه حل سروو الکتریک فقط نیاز به پر کردن مخزن کوچک روان کننده دارد و دستگاه را می توان به طور کامل، حتی از راه دور، توسط اپراتور و یک تکنسین خدمات بررسی کرد.
علاوه بر این، راهحلهای سروو الکتریک در مقایسه با فناوری هیدرولیک حدود 22 درصد زمانهای چرخش سریعتری را ارائه میدهند. فناوری هیدرولیک هنوز نمیتواند به طور کامل از فرآیندها حذف شود، اما تحقیق و توسعه ما مطمئناً به سمت استفاده گستردهتر از راهحلهای سروالکتریک هدایت میشود. مزایای بی شماری که ارائه می دهند.
زمان ارسال: مارس-23-2022